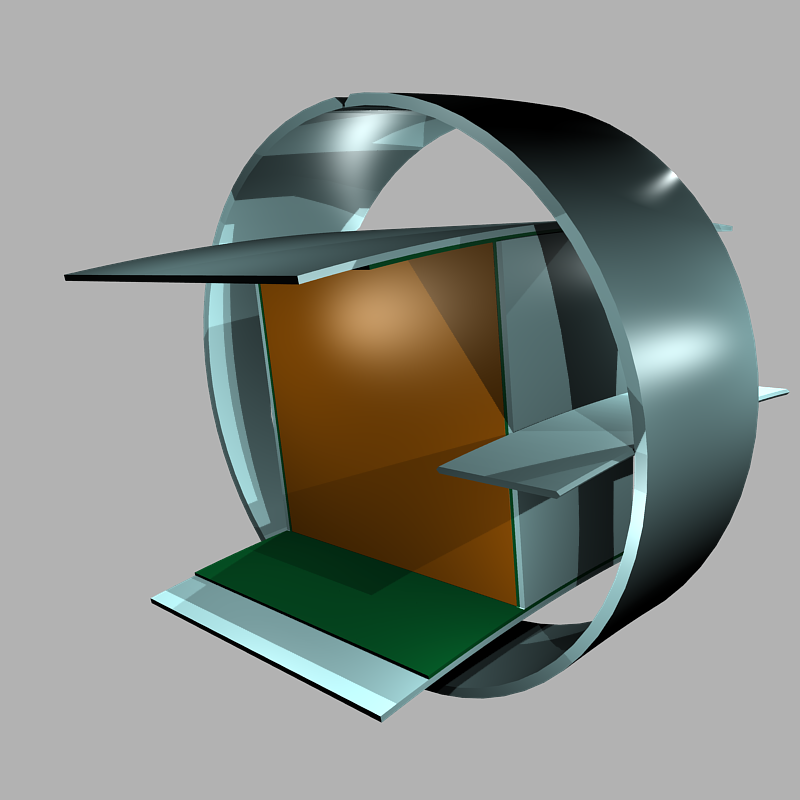
This shows a 5 degree segment of the LHe Jacket and the SC Conductor standing vertically. The center of the REACTOR is to your left. The center of the torus is straight down. Light blue designates 316SS. Brown designates the super conductor. Dark green is for electrical insulation.
This is to scale, but I am going to change a number of things, starting with the wall thickness of the jacket. Right now it is 9.5mm. I am going to change that to 10mm to take advantage of commercially available plate. This would be roughly the same as STD Wall pipe, or 3/8" wall.
There are a number of concerns when attempting this approach. Each torus will actually be two, not one wing. Each half-shell will need its own structure that renders that half-shell rigid. The two half-shells will be joined together by two seam welds to make the two pieces into a single rigid whole.
Fabricating the pieces will likely be a two step process. The plate will be cut out on a laser or plasma arc table and then sent to a CNC machine for final sizing. The inside of a torus presents us with a much more complex geometry than that found inside of an aircraft wing.
The internal structure will require a carefully written out set of assembly instructions and check list. If parts of the structure are installed in the wrong order, it will be impossible to weld some, possibly many, of the subsequent pieces.
Inspection will be time consuming and may hold up work on a single torus for hours at a stretch. It will be necessary to assemble the torii concurrently in order to balance manpower around inspection.
This kind of structure will in no way be in compliance with ASME B31.1, save possibly on the inspection procedures. This will complicate things for investors and underwriters.
As you can see, I still have a long way to go.